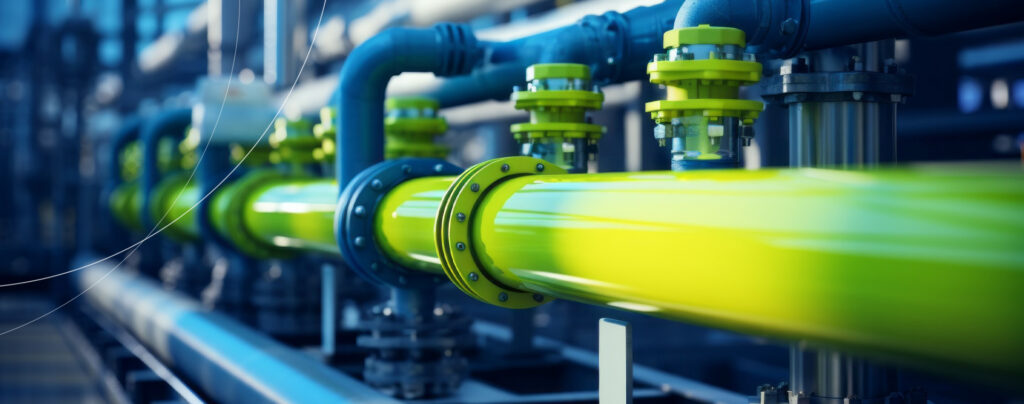
Fluenta’s FlarePhase 350 is designed to operate in extreme temperature environments, ranging from -40°C to +350°C. This broad temperature range makes it ideal for a variety of industrial applications where process conditions exceed 250°C, particularly in industries that rely on extreme thermal processes. Several key applications necessitate the use of FlarePhase 350 due to the high temperatures involved in gas measurement and emissions monitoring.
1. Ammonia Production
Ammonia production, primarily through the Haber-Bosch process, is one of the most temperature-intensive industrial operations. The synthesis of ammonia from nitrogen and hydrogen requires process temperatures between 400°C and 450°C, and the surrounding equipment, including flare stacks, experiences sustained high temperatures. Flare gas monitoring in ammonia production is critical for both safety and environmental compliance, especially given the toxic nature of ammonia and associated emissions. FlarePhase 350, with its robust design, can withstand the high heat and ensure accurate flare gas measurement, ensuring operators maintain control over emissions even in these extreme environments.
2. Petrochemical Refining
Petrochemical refineries often operate at high temperatures in processes such as catalytic cracking and reforming to break down complex hydrocarbons into more useful products like gasoline, diesel, and chemicals. These refining processes commonly operate at temperatures ranging from 250°C to 350°C, making reliable flare gas monitoring essential. Accurate measurement of gases such as hydrogen sulfide (H2S) and methane is crucial not only for process optimization but also for meeting stringent environmental regulations. FlarePhase 350 can operate in the elevated temperature zones typical of petrochemical plants, ensuring precise data for both safety and compliance.
3. Steel Production
The steel industry, particularly in processes like blast furnaces and basic oxygen furnaces, reaches extreme temperatures, often well above 1,000°C in the core of the furnace, with surrounding environments like flare stacks regularly hitting 250°C to 350°C. Monitoring emissions in steel production is critical due to the release of CO2, CO, and other potentially harmful gases. FlarePhase 350 is perfectly suited for monitoring and measuring these emissions, providing reliable data in a process that demands robust equipment capable of functioning in harsh, high-temperature environments.
4. Cement Manufacturing
Cement manufacturing is another high-temperature process, especially in kilns where raw materials are heated to over 1,400°C to produce clinker. However, the surrounding areas and gas emissions can reach temperatures between 250°C and 350°C. Emissions monitoring in cement production is crucial due to the release of CO2, a significant contributor to greenhouse gas emissions. FlarePhase 350 provides the necessary precision and durability to handle such high-temperature processes, ensuring compliance with environmental standards while optimizing operational efficiency.
5. Glass Manufacturing
The production of glass, whether for construction, automotive, or other industrial uses, involves extreme heat, with furnaces operating at around 1,400°C to melt raw materials like sand and soda ash. The flare stacks and emissions systems associated with glass production often experience temperatures within the 250°C to 350°C range. FlarePhase 350’s ability to function reliably in these elevated temperatures ensures accurate monitoring of emissions like nitrogen oxides (NOx) and sulfur dioxide (SO2), which are critical pollutants in glass production.
6. Thermal Power Plants
In thermal power generation, particularly in coal-fired and natural gas plants, process temperatures can exceed 250°C in boilers, turbines, and associated systems. Flare gas monitoring in these plants is essential for both performance optimization and environmental compliance, especially in monitoring emissions of CO2 and other gases that contribute to climate change. FlarePhase 350 can handle the temperature demands of power generation processes, providing reliable flare gas data to ensure safe and efficient operation while helping plants meet emissions targets.
7. Chemical Processing Plants
Various chemical manufacturing processes require high temperatures for reactions to occur, particularly in industries producing chemicals like ethylene, propylene, and other industrial chemicals. These processes often take place at temperatures between 250°C and 350°C, with significant gas emissions that need to be carefully monitored. The FlarePhase 350 provides the robust, accurate gas measurement needed to ensure regulatory compliance and optimize chemical production processes.
Conclusion
Fluenta’s FlarePhase 350 is essential for a wide range of industries where process temperatures reach between 250°C and 350°C. From ammonia production to steel manufacturing, cement kilns, petrochemical refining, and power generation, FlarePhase 350 provides the durability and precision needed for accurate emissions monitoring and compliance with environmental regulations. Its ability to perform reliably in such high-temperature environments ensures that industries can maintain operational efficiency and meet strict emissions standards, making it a vital tool in modern industrial processes.