“Why Flare Flow Still Defies Easy Answers” – by Dr Neil Bird, Chief Scientist, Fluenta
Accurate flare gas measurement remains one of the most persistent operational and environmental challenges in India’s rapidly expanding oil and gas industry. With stringent regulations continually evolving, companies are under increasing pressure to deliver precise and reliable emissions reporting. Traditional flare measurement technologies have consistently fallen short, struggling to cope with unpredictable gas flows, extreme environmental conditions, and shifting compositions.
In this comprehensive article published in DEW Journal, Dr Neil Bird—Chief Scientist at Fluenta—provides deep insights into the complexities and limitations of traditional flare measurement methods. Dr Bird thoroughly examines why widely used technologies such as differential pressure (DP) meters, thermal mass flowmeters, and optical measurement systems often fail to deliver accurate results in real-world scenarios.
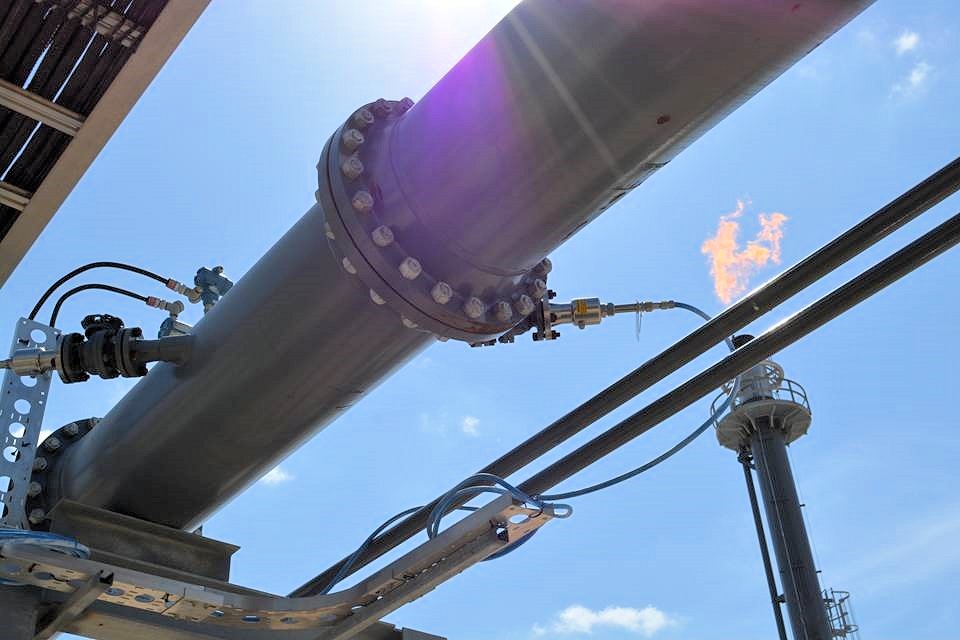
Flare Why Traditional Flare Measurement Methods Fail
Traditional flare measurement technologies like DP meters require significant recalibration due to their limited operational range. Thermal mass flowmeters rely heavily on stable gas compositions for accuracy, making them vulnerable to errors when compositions fluctuate rapidly between methane, ethane, hydrogen, and CO₂. Similarly, optical systems are severely hampered by soot accumulation, frequent maintenance requirements, and limited visibility.
The Ultrasonic Advantage
Addressing these inherent limitations, ultrasonic flare gas measurement systems emerge as a robust and highly accurate alternative. Ultrasonic technology measures gas flow by detecting differences in transit times of sound waves moving with and against the gas flow. This approach offers significant advantages:
Exceptional Accuracy: Ultrasonic systems provide accurate measurement even at extreme flow velocities exceeding 120 metres per second, ensuring reliability under all operational scenarios.
Composition Tolerance: Unlike thermal and DP technologies, ultrasonic flow measurement is unaffected by rapidly changing gas compositions, including varying concentrations of hydrocarbons, inert gases, CO₂, and hydrogen.
Non-Intrusive Design: Ultrasonic systems spool-mounted sensors, eliminating the risk of fouling, obstruction, or pressure loss associated with intrusive measurement techniques. This design dramatically reduces maintenance requirements and eliminates downtime for installation or cleaning.
Advanced Signal Processing: State-of-the-art algorithms ensure continuous, reliable data acquisition and analysis even during turbulent conditions, providing operators with real-time insights.
Real-World Impact and Regulatory Compliance
With increasingly stringent environmental regulations, accurate flare gas measurement is essential not only for operational efficiency but also for regulatory compliance. Ultrasonic flare monitoring systems provide operators with accurate emissions data, enabling them to meet or exceed regulatory requirements consistently. Companies can confidently demonstrate compliance, avoiding costly fines and penalties while improving their environmental footprint.
Fluenta’s Innovations and Solutions
Fluenta, a global leader in ultrasonic measurement technology, continues to innovate, delivering products tailored to meet industry demands. Recent developments like the FlarePhase 350 transducer system have been specifically engineered to handle severe operational conditions, including temperatures ranging from -40°C to 350°C. Additionally, Fluenta’s systems feature frequency optimization to ensure reliable performance even in flare streams with 100% CO₂ or hydrogen-rich environments, making them ideal for evolving energy transitions.
Contact Our Experts Today
Are you ready to improve your flare gas measurement practices? Submit your enquiry through our online form. One of our knowledgeable specialists will contact you to discuss how Fluenta’s innovative ultrasonic solutions can enhance your operational efficiency, regulatory compliance, and overall performance.